1. 制浆(合浆)的重要性概述
电池制浆工艺是电池制造的关键工序,是将活性物质、导电剂、黏结剂等组分相互混合、溶解、均匀分散在溶剂中形成稳定悬浮液的过程。
高能量和功率密度、高循环稳定性的锂离子电池不仅取决于优异的活性物质、电解液等材料, 也与电池的制造工艺及装备息息相关。 特别是动力和储能应用需要大量的单体电池串并联成组, 需要高精度保障单体电池的一致性, 避免“短板效应”带来的模组容量损失和循环寿命衰减, 保障电池的安全性。对于电池模块, 每个单体电池承受相同的电流, 其电压是所有单体电池的总和, 因此电池模块容量、电化学性能受限于模块内最弱的单体电池。
理想的电极浆料应具有优异的流变特性, 后续才能稳定、均匀地涂覆在集流体表面, 同时保证固体颗粒分散均匀与稳定, 不自发产生沉降与团聚, 能形成互相连通的电极微结构。浆料混合不充分时, 活性物质和导电剂颗粒发生团聚, 与黏结剂形成较大的球状物, 无法实现稳定连接, 没有良好的离子通道与导电网络, 严重降低电极电化学性能。
锂离子电池浆料主要有水性与油性两大体系, 即采用水或有机物作为溶剂。在典型的油性体系中, N-甲基吡咯烷酮(N-methylpyrrolidone, NMP)被广泛用作溶剂, 聚偏二氟乙烯(poly(vinylidene fluoride),PVDF)和碳黑分别作为黏结剂和导电剂, 形成稳定的黏结与导电网络, 保证电极结构的机械稳定性和导电性。
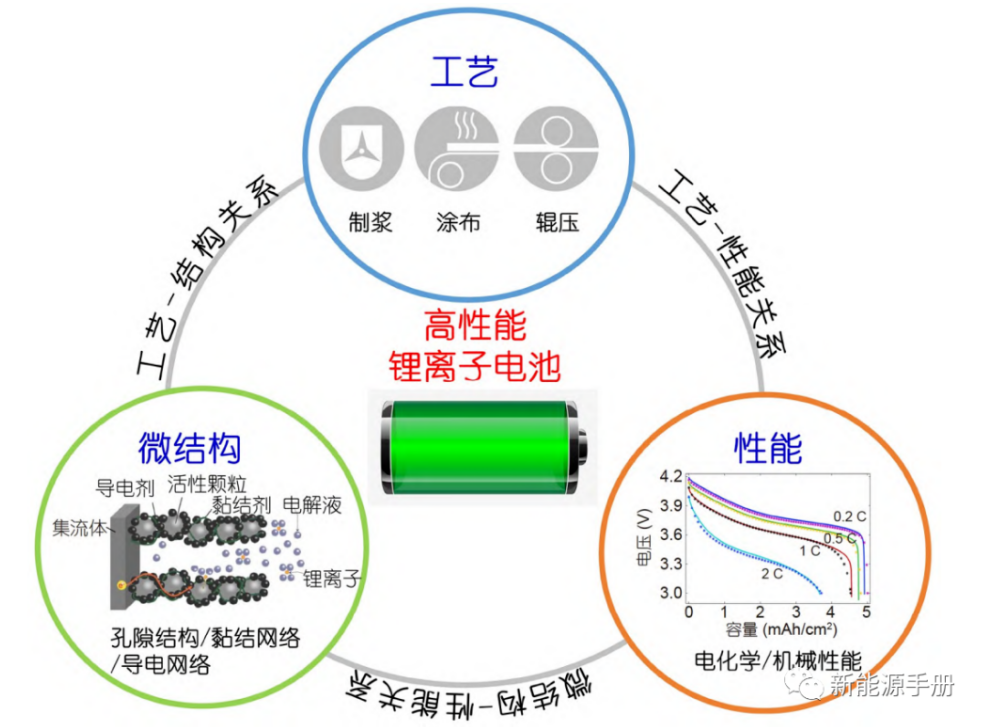
电池浆料中材料组分及其比例, 包括固含量、颗粒形状/尺寸、表面能和电子/离子电导率等, 均会显著影响其黏度、分散状态与电化学特性。除与材料特性相关外, 制浆工艺与混料顺序也是决定浆料流变特性、混合均匀度与颗粒分布状态的关键。
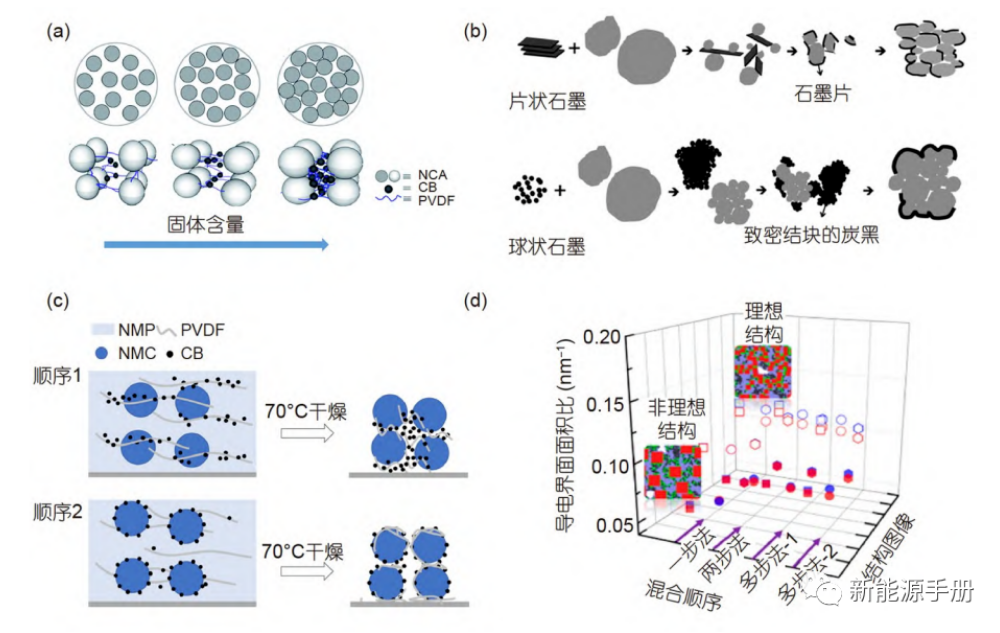
混料顺序, 即电极多组分材料加入浆料的顺序, 被大量研究证明会显著影响浆料流变特性与电极性能。一般而言, 采用多步(multi-step)混合比一步(one-step)混合方法获得的浆料黏度更低、颗粒分散更均匀, 电极性能更优异。混料顺序需要与活性颗粒、黏结剂、导电剂尺寸/形态、温度条件等多因素协同作用, 获得流变性能优异、颗粒分布均匀的电极浆料。
尽管以NMP为代表的有机溶剂已在工业电极制造中广泛应用, 但也存在成本、环境和安全问题, 如NMP在后续干燥和溶剂回收中耗时长、能耗占比高(~46.8%)。相比油性浆料, 水性浆料具有低成本、无需溶剂回收、环境友好等优势, 并广泛应用于石墨、硅基等负极浆料的制备。但水性溶剂规模化应用仍存在巨大挑战, 包括浆料与集流体间润湿性和黏附性能差、二次粒子团聚、锂离子从正极析出导致活性颗粒破坏和集流体腐蚀, 以及更严格的干燥过程(水含量<400ppm, 1 ppm = 10−6)。
2. 电极浆料研究遇到的问题
锂离子电池浆料是一种处于非平衡态的悬浮液体系。为满足各行业对高性能锂离子电池的需求,固体颗粒粒径通常很小,朝着纳米方向发展,从而导致颗粒极其容易团聚,以及浆料中各组分的分布不均匀,影响电极涂层内部的微观结构和电池的倍率性能,进而对电池的安全性和耐用性均会产生影响。在活性材料、导电剂以及集流体之间存在着导电的网络连接,浆料内部材料分散越均匀,这种网络连接的导电性也就越强,从而锂电池的性能也就越优异。因此,浆料内部物质的分散均匀性对于锂离子电池的性能有着非常重要的作用。
随着匀浆结束,搅拌停止,浆料会出现沉降、絮凝聚等现象,这对后续 的涂布等工序造成较大的影响。因而浆料在制造好之后,在涂敷之前的存储期间内必须要能够有一定的稳定性。通常,稳定性定义为浆料承受质量或相分离的能力,允许在混合步骤后长时间保持均匀的颗粒分布。
在实际情况中,浆料本身大多都是深色,用肉眼无法直接观测内部颗粒分布是否均匀,而根据其为黏性流体或胶体特性,不同的分散状态对应着不同的流变性,因此,研究者都是通过浆料的流变性能来分析浆料内部均匀性。大量研究表明,浆料的分散均匀性和沉降稳定性与原料添加顺序、溶剂种类、固含量、搅拌工艺等密切相关。
3. 正极浆料的制备工艺
3.1 湿法工艺
首先,制备聚偏氟乙稀(PVDF)胶液。使用普通的搅拌罐先打入一定量的溶剂NMP(N-甲基吡咯烷酮),将粘结剂PVDF粉体按照设计的固含量加入其中,搅拌4~6 h 后得到PVDF 胶液。PVDF 胶液为外观无色透明、具有一定粘度的液体,固含量根据需要可控制在5%~10%之间。制备好的胶液一般需要抽真空处理,并静置12 h 以上,目的是消除搅拌过程中产生的气泡。然后经密封管道通过计量泵输送一定量至浆料制备搅拌机中,加入导电剂SP,同时启动搅拌机公转(麻花桨)和自转(分散盘),公转转速设定为(25±5)r/min,自转转速设定为(500±50)r/min,并辅助NMP 喷淋,使密度极轻的SP 能够充分混合进入PVDF胶液中,搅拌时间为1 h。
其次,添加正极主材。为保证主材与胶液能够有效充分地分散,一般会分步添加,即先加入50%主材(如NCM 或LFP 等),设定(30±5)r/min公转转速和(300±50)r/min 自转转速,搅拌5 min后,再加入剩余的50%主材,辅助适当的NMP 喷淋,保持上述参数搅拌1.5 h以上。过程中根据需要,对搅拌桨进行刮桨处理,防止粘附在搅拌桨上的粉体因固液界面润湿角过大,导致无法被充分浸润[2]。
最后,将剩余的NMP 溶剂全部喷淋加入搅拌机,提高搅拌转速,自转转速为(35±5)r/min,公转转速为(800±50)r/min,搅拌10~30 min 后再将公转转速提高到(1300±50)r/min 并搅拌1.5 h,完成浆料制备。制备好的浆料在使用前需要转入中转罐进行抽真空消泡处理。
3.2 半干法工艺
半干法工艺又称“捏合”工艺,以双行星搅拌机作为制浆设备。捏合是指机械搅拌使黏性及塑性物料均匀混合的过程,包括物料的分散和混合两个过程。此工艺与湿法一样,也需要先制备PVDF 胶液,且胶液制备方法相同。主要区别在于浆料制备过程。
首先向双行星搅拌机中加入全部正极主材(如NCM 或LFP 等)和导电剂SP,仅打开设备公转,设定转速为(25±5)r/min,将粉体搅拌30min。
其次,根据主材的润湿效果,设计相应的捏合固含量,控制在68%~72%。依据设计的捏合固含量,加入一定量的PVDF 胶液和适量溶剂。考虑设备能力,防止设备高负荷运行损坏设备,可适当考虑先进行一步预捏合,即设定麻花桨反转,转速为(10±2)r/min,时间为15 min。待设备适应罐体内的粉体和胶液搅拌状态后,转入本工艺方法最关键的步骤———捏合,设定公转转速为(25±5)r/min,捏合时间为1 h。此时浆料呈现出糊状的高粘度无流动性状态。再加入剩余的胶液和适量NMP溶剂,启动搅拌机分散,设定转速为(1200±50)r/min,公转速度保持不变,搅拌运行1 h。
最后,根据浆料配方设计的固含量,加入剩余的NMP 溶剂,进一步提高分散转速至(1350±50)r/min,保持公转转速不变,继续搅拌1 h,完成浆料制备。将浆料转移至中转罐中抽真空消泡处理,真空度不超过-85 kPa。
3.3 干法工艺
此方法相比于湿法工艺或半干法工艺,制浆过程进一步简化,工艺时间进一步缩短。干法工艺省略了胶液制备的过程,采用纯干混预搅拌的方法进行制浆前粉体混合。同样是采用双行星搅拌机作为制浆设备。
首先,向搅拌机内依次加入50%正极主材(如NCM 或LFP 等)、导电剂SP、粘结剂PVDF、50%正极主材。加料过程中保持公转转速(5±1)r/min运行,加料完成后,开始干混预搅拌,公转设定反转转速(7±1)r/min运行,自转分散暂不启动,5 min后转入正常干混搅拌,设定公转转速(13±1)r/min,自转转速(400±2)r/min,搅拌0.5 h。需要确保干混能够充分混匀正极主材、导电剂SP 和粘结剂PVDF 粉体,避免下一步加入溶剂后无法得到最终稳定的浆料。
其次,对分散均匀的粉体进行NMP 溶剂喷淋,第一步加NMP 溶剂,可根据设备能力并参照半干法捏合步骤的效果,设计合适的固含量,一般同样控制在70%左右。进入粉料的润湿步骤,主要以公转搅拌为主,设定公转转速为(15±5)r/min,辅以(150±2)r/min 的自转,搅拌1.5 h。此时浆料呈现一种较高粘度的稠状液态,加入剩余的NMP溶剂,稀释并搅拌10~15 min,公转速度不变,自转转速提高到(500±5)r/min。如有必要,可在本步骤NMP 喷淋前添加导电胶液碳纳米管(CNTs)。
最后,进入高速分散降粘步骤。保持公转转速(15±5)r/min不变,提高自转分散转速至(1200±50)r/min,搅拌2 h后,降速慢搅(公转转速(10±1)r/min,自转转速(200±5)r/min)进行降温,完成浆料制备。
3.4 溶剂浸润工艺
融合干法与湿法工艺,采用“湿法不制胶”的方式进行浆料制备。无论是从工艺简化还是工艺时间角度考虑,均具有明显的优势。重点需要考虑最终浆料的稳定性。
首先,双行星搅拌机中按照固含量为70%依次加入一定量的NMP 溶剂、50%正极主材(如NCM 或LFP)、导电剂SP、50%正极主材。如有必要,可添加导电胶液CNTs。加料过程中保持公转转速(5±2)r/min 运行,加料完成后,公转转速逐步提升至(15±2)r/min,进行5 min预搅拌。
其次,直接进入高速分散步骤,公转转速为(25±5)r/min,分散转速为(1350±50)r/min,搅拌1.5 h,保持真空度不超过-80 kPa。
最后,投入PVDF 粉体,喷淋加入剩余的NMP 溶剂,如有必要可加入导电胶液CNTs。保持公转转速不变,先采用900 r/min 的自转转速进行搅拌,时间为5~10 min,完成后进入第二步高速分散,自转转速提至(1350±50)r/min,分散2 h后完成浆料制备。
3.5 双螺杆制浆工艺
此工艺与前述所有方法最大的差异在于设备的不同,此工艺采用双螺杆匹配高速分散机进行浆料制备。双螺杆设备需要配备能够较准确控制粉体和液体流速的自动加料系统。
一般情况下,为保证浆料的稳定性,会考虑先将导电剂SP 制备成导电胶液,为保证导电胶液流入双螺杆的流速控制更准确,导电胶液的粘度一般控制在2000~10000 mPa·s。
其次,设定好导电胶液、溶剂NMP 和正极主材(如NCM 或LFP)进入双螺杆的流速,流速的设定需要考虑双螺杆对粉体的预混时间、浆料配比、双螺杆预混后的粘度要求以及设备能力。双螺杆出料一般根据浆料细度评估预混效果。此时的浆料粘度超20000 mPa·s,需要通过隔膜泵进行输送。
最后,双螺杆预混出来的浆料还需要进行进一步的高速分散来降粘和降细度,最终满足使用要求。
使用双螺杆的优势很明显,可以做到连续出料,并且浆料的周转时间保持一致,从而可以保证涂布过程不会出现因浆料的批次差异导致面密度波动的异常。双螺杆的弊端也很突出:双螺杆的结构设计致使其在使用过程中不可避免地会出现较严重的磨损情况,从而影响最终电芯的性能发挥,如较大的自放电不良;其结构设计也直接导致设备清洁、保养变得较为困难。
4. 浆料分散性和均匀性的影响因素
黏度是流体黏滞性的一种度量,是流体流动力对其内部摩擦现象的一种表示。浆料的黏度通常随剪切速率而变化,该现象可对浆料中的颗粒-聚合物之间的相互作用进行详细的描述。当存在剪切变稀行为时,浆料中存在容易被剪切应力破坏的软团聚物。相反,剪切增稠的存在通常表明浆料中有着硬聚集颗粒。黏弹性也是流变学重要的参考参数。通过储能模量(G′)和损耗模量(G″)的相对值来表征浆料的黏弹性特征。储能模量G′又称为弹性模量,代表浆料发生可逆弹性形变时所储存的能力,是浆料弹性变形的度量。损耗模量G″又称为黏性模量,代表浆料发生不可逆变形时消耗的能量,是浆料黏性变形的度量。损耗模量G″又称为黏性模量,代表浆料发生不可逆变形时消耗的能量,是浆料黏性变形的度量。在频率扫描中,基于G′和G″的相对大小,并评估G′对角频率的灵敏度,能够反映出浆料是流体状态还是类固体状态的信息。并且在低频范围下,G′>G″且其差值越大,表明浆料的稳定性越好。较为少见的是幅度扫描测试。在幅度扫描中的低应变下,G′>G″且G′的值保持相对恒定,这表明浆料内部存在着网络结构,且该网络结构是完整的。该凝聚网络区域成为线性黏弹性区域,并且G′的常数值被称为平衡存储模量(G′0),描述网络结构的强度。另一种流变性质是屈服应力(σ0),表示诱导浆料流动所需的最小力。
研究颗粒-聚合物体系的内部结构和分散状态的广泛方法为流变学。如果颗粒之间存在牢固的结合,彼此之间没有很好的分散,通过流变学特性发现固体或凝胶状行为,且其黏度很高。相反,当浆料充分分散时,将出现类似流体的行为,并且黏度将大大降低。
4.1 活性物质对浆料流变性的影响
活性材料的表面状态会影响着浆料特性和分散状态。颗粒的表面包覆碳上存在着众多的碳衍生物,如羧基、羟基和羰基等有机官能团,这些官能团间的相互作用导致颗粒在水基浆料中的凝胶化。极高的固体负载量,未分散开的颗粒形成的团聚体所造成凝胶化。表面的碳衍生物的减少有利于颗粒的解凝胶,使得浆料由凝胶状态转为分散状态。
活性材料颗粒的尺寸大小对浆料的分散性和稳定也有着重要的影响。以颗粒尺寸分别为130nm的LiFePO4(LFP)和8.9μm的镍钴锰酸锂(Li(Ni,Mn,Co)O2,NMC)为活性材料研究正极浆料的流变性和稳定性。LFP浆料存在较为明显的剪切变稀行为和屈服点,即LFP浆料形成了典型的凝胶类型结构。这是因为130nmLFP颗粒具有大量的相互作用位点,特征直径在100~200nm的聚偏氟乙烯(polyvinylidenefluoride,PVDF)分子链形成了更平坦的构型,降低与其他颗粒间直接接触的可能性。在浆料分散体中由PVDF和固体颗粒之间的吸引力形成了凝胶网络结构。
和细小的LFP颗粒相比,具有相同固含量、由颗粒尺寸更大的NMC制备的浆料有着更低的黏度,仅存在轻微的剪切变稀行为,且无屈服点。这是流体系统的典型行为将NMC体积分数升至30%时,该浆料的黏度会显著升高,但仍没有屈服点,表明该浆料也是典型的流体性系统。这是因为NMC颗粒尺寸为8.9μm,PVDF分子特征尺寸远小于NMC颗粒尺寸,很大一部分的黏结剂会沉降在与下一个颗粒距离很远以至于不能形成桥接作用的位置,无法形成有吸引力的网络结构。最终无法形成稳定的聚合物凝胶结构。当NMC颗粒增多虽能让结合键数有所增加,NMC颗粒网络结构的整体吸引力相互作用有所增强,但在低剪切速率下也能诱导结构分解,无法形成稳定的凝胶。由弱吸引力形成的凝胶网络可以固定颗粒以实现颗粒系统的稳定均匀化,但必须适当调整吸引力,既要防止因形成过于坚固的凝胶网络而无法达到电极涂覆过程中完全流化的要求;也要避免所形成的凝胶结构强度过弱而无法抵抗离散粒子的沉降。
4.2 黏结剂对浆料流变性的影响
黏结剂含量对浆料的流变特性有着重要影响。定义SBR在SBR/CMC中的占比为[SBR]。如下图所示,[SBR]为90%和70%时浆料的黏度曲线都比较复杂,在低剪切区域呈现剪切变稀,在高剪切率下呈现剪切增稠。随着[SBR]的减小,浆料的表观黏度增大,剪切变稀现象更明显。图(b)中的相对黏度排除了SBR和CMC的流变本质特性对浆料流变的影响。很显然,浆料的相对黏度随着[SBR]的减小而降低,表明[SBR]的下降有利于浆料中电极颗粒的分散。此时仍可观察到[SBR]较高时浆料存在复杂的流变行为,表明浆料中的电极颗粒同时存在着软团聚体和硬聚集体。当[SBR]为50%时,浆料仅表现出剪切增稠行为。当[SBR]为30%和10%时,浆料表现出牛顿流体行为,浆料中的固体颗粒分散性能优良。
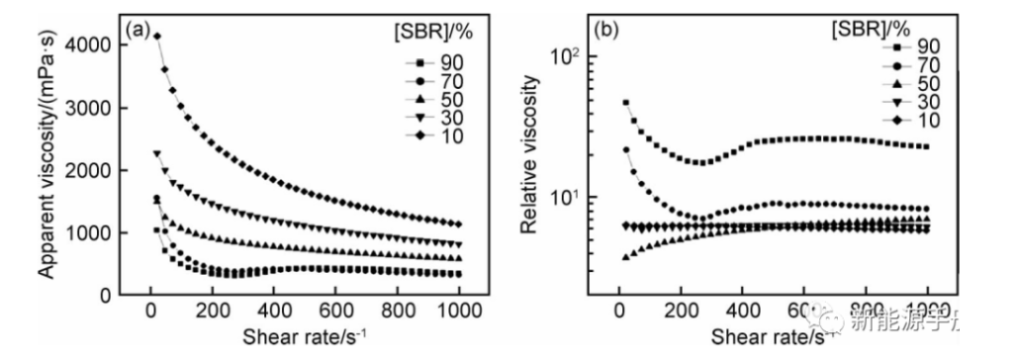
(a)表观黏度;(b)相对黏度
电极颗粒上的黏结剂吸附量随着[SBR]减少而降低,有更多自由的黏结剂在干燥过程中随着水分子迁移到电极表面。因此,当[SBR]减少时,电极中黏结剂分布的均匀性会下降,极片顶部(95%)和底部(5%)位置黏结剂含量的差异增大。黏结剂分布均匀性的降低导致极片的黏附力降低,即[SBR]较低时,极片较差的黏附性主要归因于电极片中黏合剂分布均匀性的降低。
黏结剂的浓度和种类均会影响浆料的流变性能和微观结构。
4.3 导电剂对锂电池合浆工艺及性能的影响
导电剂的类型选用,在合浆过程中的添加顺序和分散工艺,对制备的电极浆料、电极片和电池性能的影响显著。电极中电子传导可以用渗透理论来解释。在该理论中,导电物质作为连续相,但相间存在电阻,而导电剂的形貌千变万化。因此,导电剂的形貌对于浆料性能的影响至关重要。目前碳系导电剂为锂电池化学体系中最常用的导电剂,主要包括导电石墨、导电炭黑和导电碳管等。
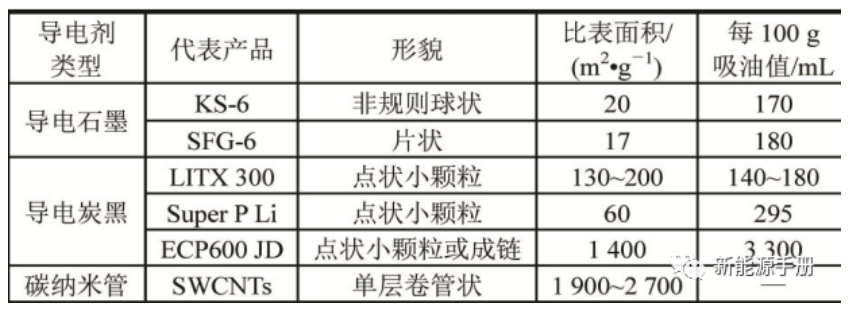
根据电池产品性能需求进行电极配方的设计,选用适当和适量的导电剂非常重要。一方面要求导电剂用量可以尽量减少,以增加活性主材的用量来提高电池能量密度;但另一方面要求电极的电导率要高,以保证电池的倍率性能及高低温循环性能不受影响。在导电剂选用方面,粒径小、比表面积大的导电剂,虽然可以实现在更小用量下更好的电导率提升作用,但是其在制浆过程中非常难以分散,浆料粘度明显升高,导电剂的团聚现象也随之发生,在电极涂覆过程中极片出现外观不良,如图所示,导电剂未分散均匀而出现局部团聚。
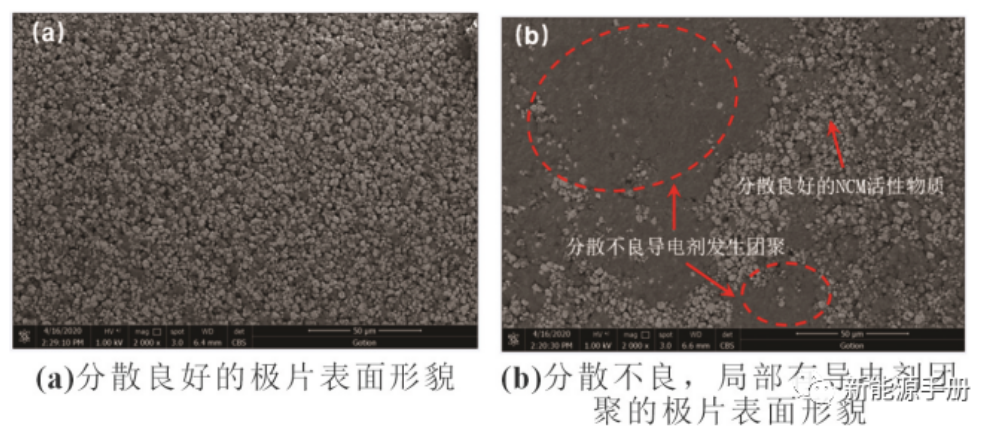
因此,平衡导电剂的配方用量与电极的电导率性能、制浆分散效果,就成为了导电剂的选用准则。随着导电剂供应商新工艺技术的开发以及分散技术的提升,一些预制导电浆料的出现改变了导电剂在合浆工序分散的现状,例如碳纳米管导电浆料,其具有良好的预制分散和稳定性,合浆过程只需将导电浆料投入混合均匀。
在合浆工序中,影响导电剂分散效果的工艺条件主要为导电剂的加入顺序、分散速度和分散时间等。通过提高分散速度和延长分散时间可以提高导电剂的分散效果,但是如果导电剂表面润湿性不充分,分散剂未充分发挥作用,导电剂颗粒仍会发生聚集并形成团聚体,从而影响电解液在电极内的分布状态。电解液会富集在电极中导电剂含量过高的区域,而电解液贫瘠处锂离子迁移扩散速率将受到影响,因此造成的极化现象将劣化电池循环寿命等电性能指标。
在前述的干法和湿法两种合浆工艺中,导电剂的加入方式与顺序将影响其分散效果,进而影响活性物质与导电剂间的导电网络形貌,电极电阻率和电池的电性能也随之发生变化。在干法合浆过程中,导电剂与活性物质的预混可以增加导电剂与活性物质的接触点,形成了良好的短程导电网络;预混干粉进入溶剂后,由于液相中“游离”导电剂的数量有限,制备的电极电导率会有所下降,全电池会表现出较高的直流内阻。而采用湿法合浆工艺的浆料,由于分散剂或胶黏剂先被制成胶液,然后导电剂和活性物质分别加入胶液中进行分散,和干法合浆相比,湿法合浆导电剂会更多地“游离”在胶液中,导电剂和粘结剂形成的网络结构将活性物质包裹,因此制备的电极电导率会得到提升,全电池表现出更小的直流内阻。因为湿法合浆需要预制胶液,该工艺虽然对设备的剪切分散能力要求较低,但是合浆时间较干法合浆更长。
总体而言,锂离子电池中使用的导电剂可有效提高电子传输速率,降低电极和全电池电阻率,对全电池的电化学性能有着显著影响。不同类型的导电剂因其形貌、比表面积、吸油值等特征性能参数不同,其加工性能也各不相同。合浆设备的迭代升级,实现了锂电池合浆工序的效率提升及制造成本降低;新型导电剂的开发与使用,配以优化的合浆工艺,可以有效改善导电剂的分散状态、提升浆料性能,最终实现全电池的产品性能和产品一致性提升。
4.4 溶剂对浆料流变性的影响
种类繁多的黏结剂的亲水性能存在差异。根据黏结剂的亲水性来选择适合的溶剂可以提高浆料的分散均匀性。溶剂的种类会对浆料的流变性产生影响。
有机基浆料更好的流动性会使得该浆料中的石墨更容易与溶剂一起流到干燥电极片的顶部,从而造成电极片成分不均匀,另一方面,由水基溶剂浆料制备的电极片中成分的分布会相对更均匀。在有机基电极片的顶层上可观察到大量的石墨,其几乎覆盖了其他成分,而在其底层发现石墨含量很少。对于水基电极片,顶层和底层的石墨含量之间的差异不太明显。主要是因为有机浆料的低黏度和高流动性使得石墨在干燥过程中重新排列。并且有机基电极片的成分不均匀分布会使其电阻和充电放电效率方面的性能比水基电极的性能差。
溶剂浓度较高的浆料分散体有着很低的屈服应力并表现出牛顿行为,溶剂浓度相对较低的浆料有着更高的屈服应力并表现出剪切变稀行为。这是典型的絮凝分散体浆料,其中存在于颗粒之间的弱吸引力形成了絮凝物的颗粒簇。超过临界浓度时,絮凝物在整个浆料体系中相互连接,从而形成薄弱的网络。屈服应力便是浆料中存在网络结构的体现。随着溶剂浓度的降低,整个浆料系统的连通性和其屈服应力都会增加。相反,在稀释的浆料分散体中,絮凝物以独立个体存在,未能形成网络结构,浆料保持液体特性,且无屈服应力。
4.5 分散添加剂对浆料流变性的影响
分散添加剂在浆料的制备过程中对颗粒团簇的分布状态有着重要的影响。可以通过毛细管力来控制浆料流变性能。在浆料中采用CMC水溶液作为溶剂,加入少量的与水不相溶的正辛醇,利用CMC水溶液与正辛醇对浆料内部固体颗粒间接触角的不同,使得浆料内部产生毛细管力,进而控制浆料的流变性能和悬浮稳定性。 浆料黏度会随着固含量的增加而上升,且都存在着剪切变稀行为。
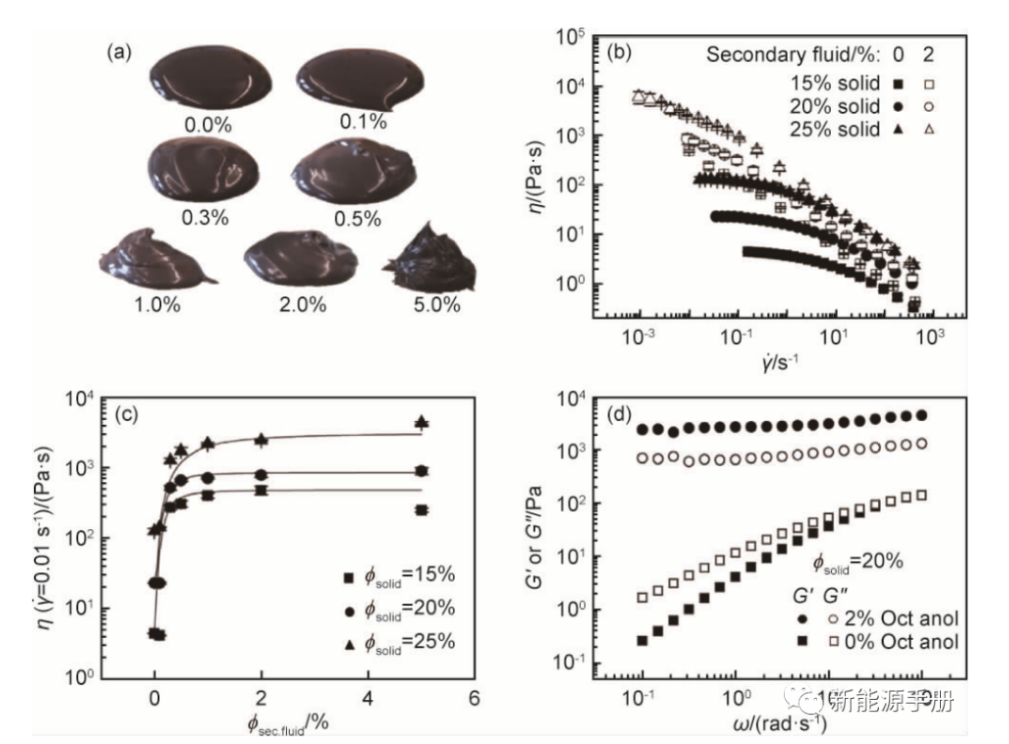
总体来说,分散添加剂对浆料的分散均匀性和沉降稳定性的影响方式主要是改变溶剂和颗粒表面的接触角和通过静电作用力阻碍团簇的合并。颗粒表面和溶剂之间的接触角越小,溶剂对颗粒表面的作用力就越大,从而使得粉体的分散效果更好。分散添加剂能够降低这两者的接触角、减小团聚体内部作用力和颗粒-溶剂作用力之间的差值,有利于团聚体的分散。但分散添加剂并不能使三相接触角为零,故粉体的分散仍需要输入其他方式的能量才能达到最佳效果。在浆料中,团簇的尺寸和形貌、活性物质和导电剂的分布,都受到相互碰撞的团簇的重组过程控制。阴离子或阳离子分散添加剂通过静电作用力来改变团簇内部的作用力,阻碍团簇合并。分散添加剂的选择应避免其在干燥电极中的残留和对铝集流体的腐蚀。
4.6 pH值对浆料流变性的影响
如果浆料溶液为弱酸性,因此溶液中沿聚合物链的未离解的羧基彼此缔合以形成氢键。每个聚丙烯酸酯分子形成随机卷曲的结构,进而溶液显示出低黏度。添加NaOH之后,溶液内相关组分的电离度增大,导致相邻离解的羧基之间由于静电作用相互排斥,聚丙烯酸酯链被拉伸,导致溶液黏度增加。黏结剂黏度的增加有利于电极内部活性物质的均匀分布。
有报道指出,在较高的pH值下聚丙烯酸PAA中羧基的离子化程度更高,因此它们的迁移率受到很大限制,可能导致黏度大大提高。此外,所有溶液中都存在着剪切稀化。在低剪切速率下较高的连续相黏度可减缓悬浮颗粒的沉降和聚结来提高水性悬浮液的稳定性,而在高剪切速率下发生的剪切稀化使浆料在制备过程中更容易混合,这对于生产高质量层压板很重要。因此,在低剪切速率下足够高的黏度与剪切稀化相结合是Si纳米颗粒在高浓度悬浮液中共混以进行大规模层压工艺的理想组合。
4.7 温度对浆料流变性的影响
浆料内物质之间可能会受到黏性力、布朗运动等的影响而影响其分布,这其中温度对于细小颗粒布朗运动的影响尤为显著。
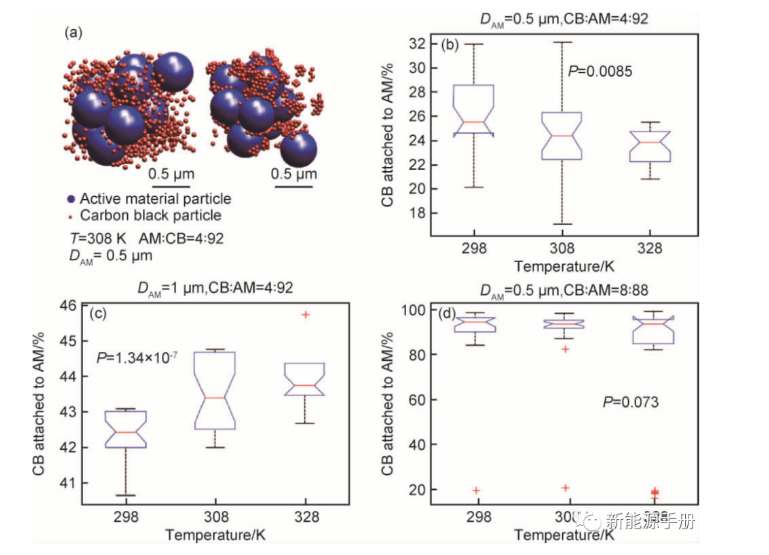
4.8 混合步骤对浆料流变性的影响
浆料中的液体组分扩散到固体颗粒的内部区域孔隙中,不同的混合条件可以引起液体吸收程度的偏差。粉末的不同比表面积和液体吸收程度会加大这种差别。据报道,在浆料的制备过程中,即使使用相同种类和数量的导电剂、活性材料、黏结剂和溶剂等原材料,不同的混合顺序会对浆料的性质及电极的性能都产生影响。
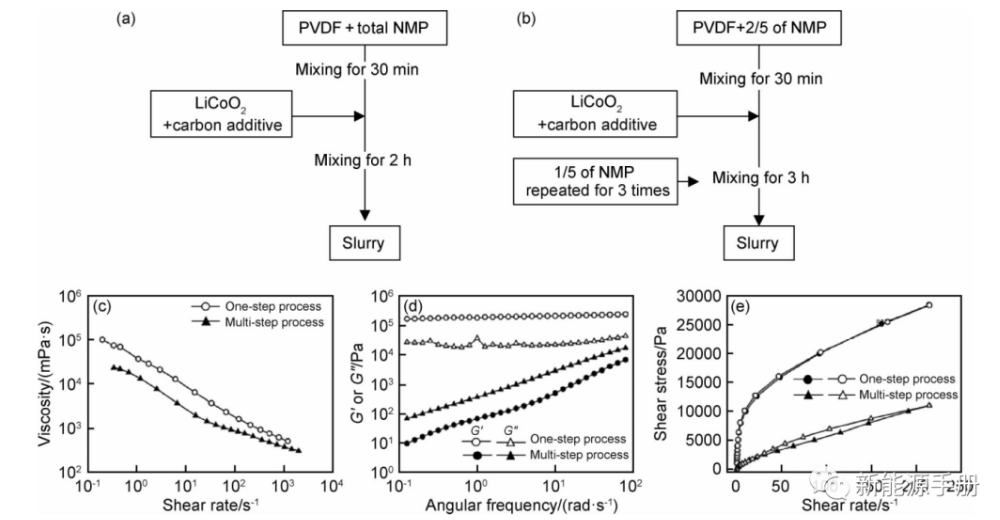
(a)一步法;(b)多步法;(c)黏度随剪切速率的变化;(d)黏弹性模量随角频率的变化;(e)两种制备步骤下浆料的流动性能
5. 锂电池电极浆料评价方法
5.1 粘度/ 流变特性
液体在流动时, 分子间会产生内摩擦, 把这种性质称为液体的粘性, 用粘度数值大小衡量表示。粘度的定义公式(牛顿公式)如下
粘度= 剪切应力/ 剪切速率
剪切应力是指流体在剪切流动中单位面积切线上受到的力, 如图所示, 剪切应力=f/s。
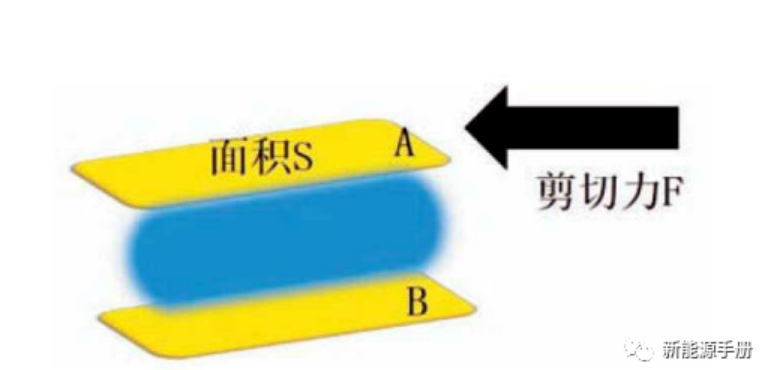
剪切速率是当将流体视为无数层组成时, 描述层与层之间运动梯度的值。
5.2 流变曲线
剪切速率或剪切应力之间的函数关系曲线称为流变曲线,常用来描述浆料(流体)粘度随剪切特性的变化规律。用流变曲线可以区分流体类型a牛顿流体在流变曲线上,剪切应力与剪切速率间的关系为一通过原点的直线关系。生产中常用粘度计、流变测量仪来测量粘度和流变曲线,其中粘度计操作简单,流变仪能够测量较大范围、更全面的粘度-剪切速率/应力曲线,并且测量结果也更加精确。电池浆料作为一种非牛顿流体,具有剪切变稀、粘弹性、触变特性等多种流变特性。
5.3 剪切变稀
大多数锂离子电极浆料具有剪切变稀的特性, 如图所示剪切粘度随剪切速率的增大而减小M。这种特性在固体含量较高的浆料中更为明显。在较高的剪切速率下,强剪切力会破坏材料之间形成的网络结构, 使颗粒重新排列成更有序的平行于剪切场的结构,导致粘度下降,在较高的剪切速率下达到牛顿平台。
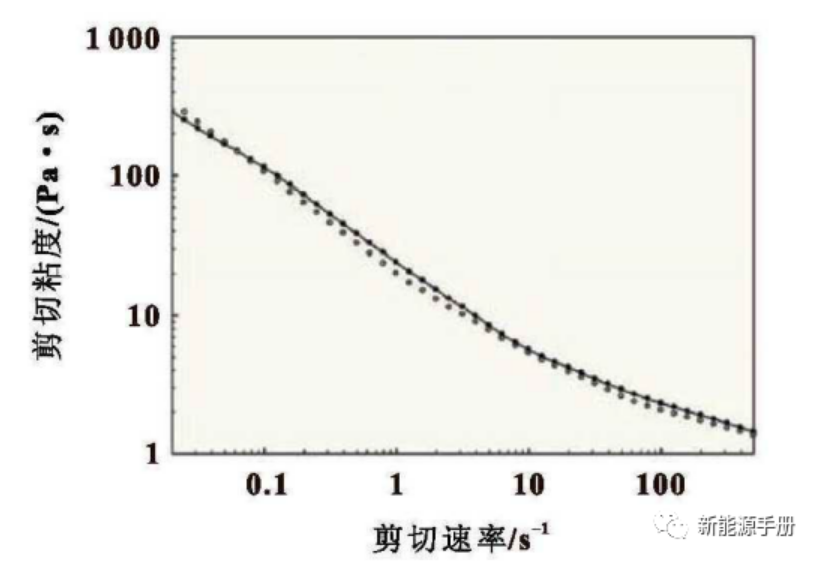
5.4 粘弹性
粘弹性也是衡量浆料性质的一个重要参考标准, 展示的是浆料粘性(液体)和弹性(固体)之间的联系,简单来说就是表征浆料更像液体还是固体。若锂电池浆料只有粘性而没有弹性,那么涂布时就会出现严重拉丝,不能获得好的涂布效果,因此,要保证锂电池浆料除了粘性之外还要具有一定程度的弹性,使涂布过程中分裂的丝状物迅速回弹,保证涂布均匀。若浆料弹性非常大或完全没有粘性,表明浆料团聚十分严重,或者类似固体,此时,浆料将完全不能涂布。
5.5 触变性
剪切速率从零不断增大至一个定值,并在该过程中记录下对应的剪切应力, 然后剪切速率再逐渐减小至零,同时记录对应的剪切应力值,以做出剪切速率-剪切应力的封闭曲线,该曲线称为触变法环。法环面积越大,代表触变性能越大,反之则越小。
5.6 粘度变化
粘度是评价锂离子电池浆料稳定性的重要依据M。粘度太高或太低都不利于涂布, 粘度高的浆料不易沉降且分散性较好,但是粘度过高时流平效果差, 造成涂布困难,降低涂布速度, 适当降低粘度有助于提升涂布效率;粘度较低时, 浆料流动性好且有助于浆料脱除气泡, 但是太低时会导致干燥困难,降低涂布速度,加剧涂布量不均勻现象,还可能出现涂层龟裂、楽料团聚等问题。
5.7 固含量
活性物质、导电剂、粘结剂等固体物质占整个浆料质量的百分比称为浆料的固含量。—般情况下的固含量在40%-70%区间内。固含量测试方法主要为烘干法。利用水分测试仪可快速且相对准确地测量浆料的固含量, 水分测试仪采用加热失重的原理,通过卤素灯将样品均匀加热使样品中的溶剂蒸发, 通过加热前后的质量变化计算固含量。
5.8 浆料的粒度(细度)
粒度是检测浆料均匀性的一项重要指标。均匀度即浆料在空间分布上的一致性, 颗粒团聚严重的样品均勻度通常较差。采用刮板细度计来表征浆料的粒度。
5.9 ERT粒子团聚或评价粒子分散状态的测量
锂离子电池阴极以锂钴氧化物(LiCoO2)粉末作为阴极活性材料,炭黑(carbon black,CB) 粉末作为导电助剂,将两种颗粒溶解在有机溶剂中制成阴极浆料。之后将阴极浆料涂覆在铝箔(集电器)上干燥形成薄膜,从而制成阴极极片。在阴极浆料中,炭黑颗粒通常用于弥补阴极材料导电性差的缺陷,并且还提供与电极内的电子导电路径相关的导电网络。炭黑颗粒必须均匀分布在每个活性颗粒周围,它们的均匀性直接影响最终的电化学性能。因此,研究一种能够检测锂离子电池阴极内粒子团聚或评价粒子分散状态的测量系统极为重要。
公开报道中,可将扫描电子显微镜方法和电阻抗谱方法结合来评估浆料的色散状态。利用扫描电子显微镜研究了阴极浆料中的粒子特性,并重点研究其物理性质。或利用Stokes 理论(即粒径较大的粒子沉降速度较快),用离心沉降搅拌法评估粒子在阴极浆料中的分散特性。还可以建立了一种在阴极浆料干燥前应用电阻抗谱法检测阴极颗粒团聚的方法,通过等效电路通过拟合来验证此方法的正确性。然而,这些方法不能应用于阴极浆料制备过程,因为实验样品是在搅拌和评估后从阴极浆料中提取的。
过程层析成像(processtomography,PT) 是一种可视化多相流中粉末颗粒浓度分布的方法。PT方法通过测量目标的各种物理量,将目标区域的密度分布输出为图像。PT方法能够检测生物体或植物流道中多相流中的特定物质。其中,电阻层析成像(electrical resistance tomography,ERT)方法是通过在多个电极之间施加电流和测量电压来获得电导率分布图像的方法,适用于检测电导率差异很大的物质。
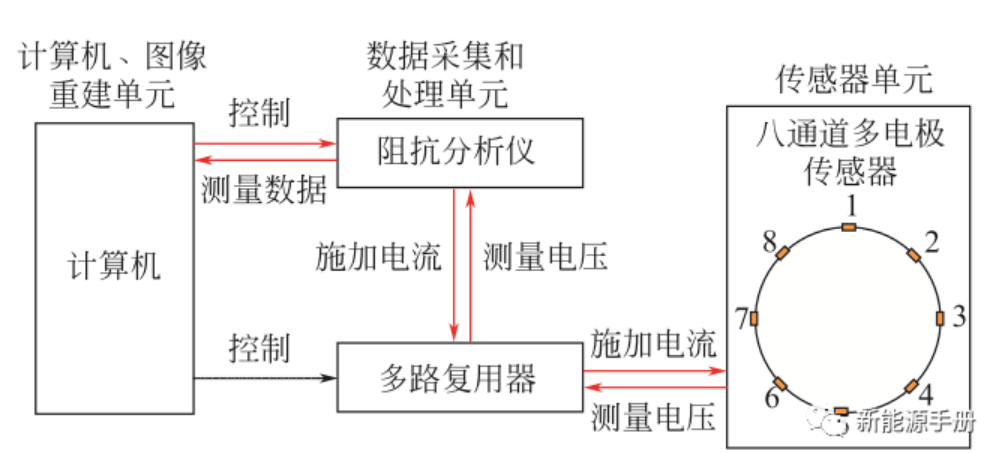
ERT的原理是在拟稳场中,利用不同媒质具有不同的电导率,判断出敏感场中媒质电导率的分布情况。由计算机(控制单元)向数据采集和处理单元发送控制信号,对任意一对电极施加激励电流,使被测对象内部建立敏感场。通过变更多电极传感器电极对,循环检测相邻电极对的电势差,获得不同方向上的电导率分布。数据采集和处理单元将收集到的测量信息传送至计算机,计算机根据一定的算法将测量数据重建成场域分布图
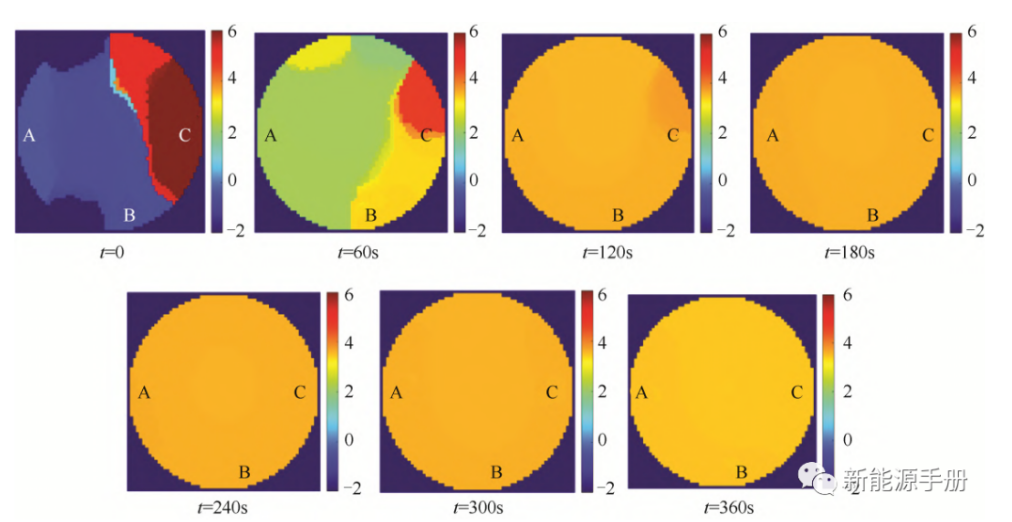
上图显示了使用ERT方法和PD-IPM算法重建的锂离子电池阴极浆料电导率重构图像。在图中,以搅拌时间t 为实验条件对浆料样品进行分析。当搅拌时间t=0时,图像C区呈现电导率较大的深红色,A、B区域呈现电导率较小的深蓝色,电导率较大的CB 颗粒团聚分布在C 区域, 电导率较小的LiCoO2 颗粒团聚分布在其他区域;当搅拌时间t=60s时,C区域颜色为红色,其余较大区域显示为绿色,少部分为橙色与黄色,这说明浆料在搅拌60s后分散度不高,电导率分布不均匀,呈现C区分布电导率较大的CB 颗粒团聚,其他区域分布LiCoO2 和CB 粒子团聚的混合物;当搅拌时间t=120s时,图像颜色统一为橙色,C区有小区域颜色较深,此时的浆料中LiCoO2和CB粒子的均匀度有所提升,电导率较一致;当搅拌时间t 继续增加,图像颜色不发生变化,证明此时浆料的分散度在此实验条件下达到最高,电导率趋于一致且不再随搅拌时间t 变化。
6. 提高电极浆料性能的策略
由于范德华力或静电吸引力以及重力作用的存在,浆料中的颗粒很可能会发生团聚或沉降。这大大影响了浆料组分的分散均匀性和浆料整体的抗沉降稳定性。在水系浆料中更容易存在相对较强的氢键和静电力,这为颗粒的团聚提供了有力的条件。因此,水系浆料通常需要添加分散剂,以提供静电屏蔽的方式来防止颗粒的团聚,使导电剂和活性物质分散得更均匀。此外,还可通过添加表面活性剂,以改变团簇内部的作用力来改变接触角方式,提高水系浆料的均匀性。但表面活性剂可能在浆料干燥之后仍然存在于电极颗粒的表面,这不利于电极的电导性。故应选择在干燥过程中容易挥发的表面活性剂。在油系浆料中,可以通过黏结剂的分子量和颗粒-黏结剂相互作用的强度,使得黏结剂的垂悬端相互缠绕成网络,形成桥连絮凝。这些跨越体积的网络有利于提高浆料的抗沉降性。而在水系浆料中则要避免形成这种聚合物网络结构。
所制备浆料的性能还与其投料顺序有重要关系。对于粉体颗粒的投放,多步添加制备的浆料中组分的分散比一次性添加制备的浆料中组分的分散更均匀。在水系浆料中最常用的黏结剂为CMC和SBR,这两种黏结剂的分散能力存在着较大的差别。因此,黏结剂的混合顺序对于水系浆料的影响十分明显。CMC的分散能力高于SBR的分散能力。但对于磷酸铁锂,SBR的吸附竞争力远高于CMC。因此,制备磷酸铁锂浆料时应该先放CMC后放SBR。而对于石墨类的负极材料,CMC的吸附竞争力高于SBR。因此,制备石墨浆料时这两种黏结剂的投放顺序影响不会很大,但SBR只在CMC含量很低时才能起到分散作用。
最后,其他一些因素也会影响锂离子电池浆料的性能,如pH 值、温度。此时,应该考虑浆料中的AM的种类、导电剂的大小、黏结剂的分子结构来综合进行选择,以便制备出性能优良的浆料。
参考资料:
- 孙晓辉,曾红燕,李景康. 浅谈锂离子电池正极浆料的制备方法及其特性[J]. 浙江化工,2022,53(3):12-16
- 王海波, 曹勇, 王义飞,等. 导电剂对锂电池合浆工艺及性能的影响[J]. 电源技术, 2021, 45(11):3.
- 王志龙, 刘晓栋, 赵桐, 等. 锂离子电池阴极浆料内导电粒子动态分布的可视化[J].,化工进展, 2021, 40(12): 6505-6515
- 李茂源等,
- [J].,科学通报,2022 年第67 卷第11 期: 1088 ~ 1102
- 欧阳丽霞, 武兆辉, 王建涛. 锂离子电池浆料的制备技术及其影响因素[J]. 材料工程, 2021, 49(7):14.
- 郭勍、杨雪莹、郑海山、荆有泽、苏晓倩. 锂电池电极浆料评价方法[J]. 电源技术, 2020, 44(10):5.